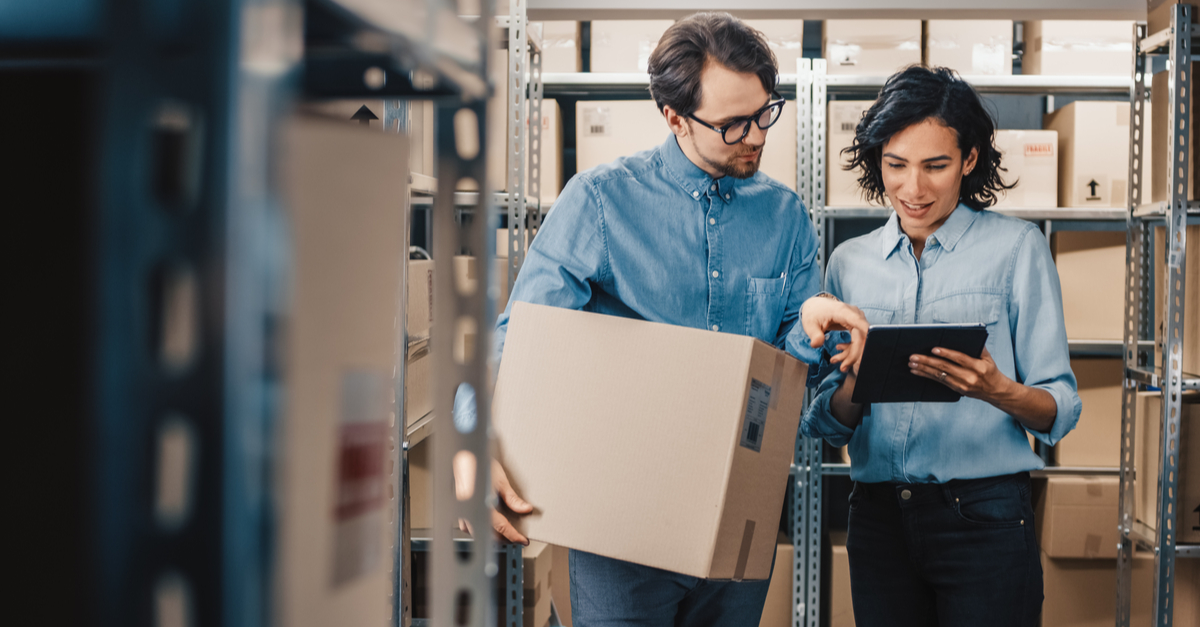
Inventory Management: We Can Do Better
Each day through the COVID-19 pandemic, I tune into Anthony Cuomo’s (governor of New York) daily briefings. It is my break in the day. As a multi-tasker, when Governor Cuomo broadcasts, I use the time to work out on my rowing machine.
His opening line is, “Let’s start with facts. While we all have opinions, let’s start by reviewing the facts.” When he says this, I smile and row harder. I wish that all discussions could start with the facts.
Reflection
In my day-to-day work in supply chain management, I find more encounter more opinions than facts. …most discussions are fueled by over-zealous and self-serving marketing programs. Strong opinions and egos (mostly male) abound… For over two decades, I obediently tapped my foot to technology leaders’ glibly spouting opinions. I seek facts, but I find that they are few and far between.
The lack of fact-based discovery makes me itch…
A Story
Last week on my Network of Networks call, a proud technology salesperson, let’s call him Jim, announced, “I am speaking at Logimed next week on the impact of Just-in-Time (JIT) on the COVID-19 response. Downsizing inventories over the past decade crippled the response.” As I heard Jim speak, I twisted in my seat unsure what to say.
I struggle when I hear opinions that don’t align with facts. So, let’s start with the data. (Yes, am that geeky kind-of-gal that likes to ground discussions in data.) In Table 1, I share research collected for the Supply Chains to Admire analysis on the average days of inventory by industry across the period of 2004 to 2019 by increments to match economic shifts. The period of 2007-2008 was the downturn of the recession while the period of 2009-2013 marked the recovery. (The source of this data is a syndicated data provider of public reporting termed “Y-Charts.”)
So when we start with the facts, it is clear that every industry peer group increased the days of inventory. In addition, each peer group is markedly different. So, why have we not reduced inventory?
Now I will share my opinion.
- Complexity. Supply chain leaders in the beverage and household products industries struggled to manage complexity.
- Supply Chain Leadership. With average operating margins of 20-22%, medical device and pharmaceutical companies are supply chain laggards.
- Supply Management. Industries like automotive pushed cost and waste backward in the supply chain.
- Network Design. Only 9% of companies actively design the supply chain with a focus on buffer design.
- Factory Scheduling. With the evolution of the advanced planning market and the growth of the market share of ERP expansionist companies, solution capabilities in factory scheduling weakened.
- Executive Understanding. Many executives do not understand the form and function of inventory and the need for inventory buffers.
- Balance in S&OP. While 82% of companies have an S&OP process, less than 50% of company processes are balanced and only 1/3 of companies actively run “what-if” scenarios.
Read more at Inventory Management: We Can Do Better
Leave your comments below and subscribe us to get updates.