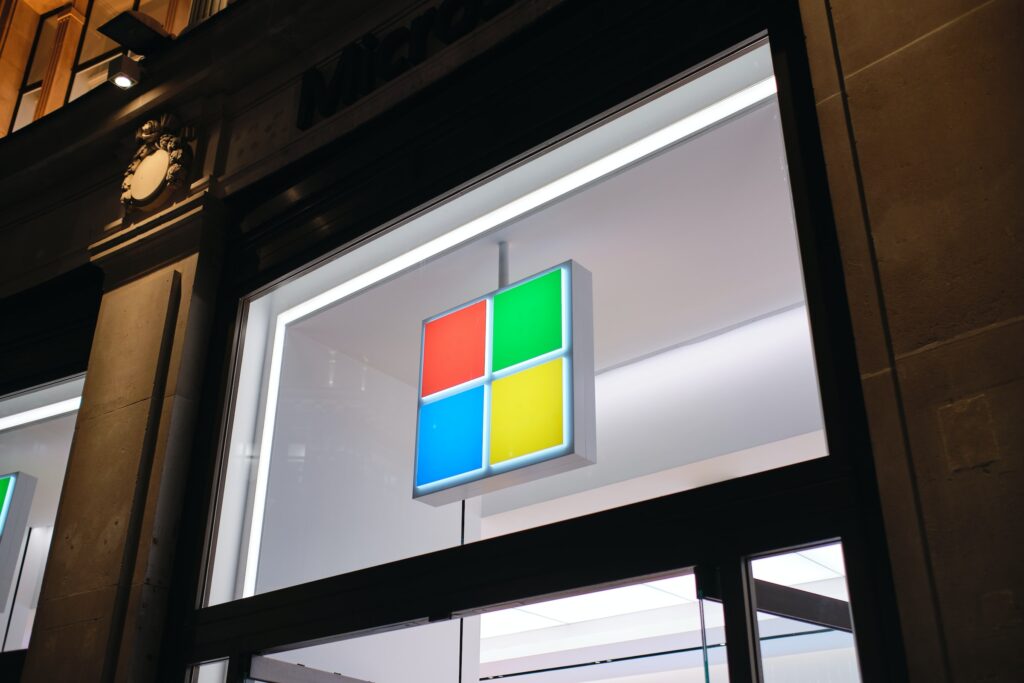
Microsoft announces the Microsoft Supply Chain Platform, a new design approach for supply chain agility, automation and sustainability
Microsoft Corp. announced the Microsoft Supply Chain Platform, which helps organizations maximize their supply chain data estate investment with an open approach, bringing the best of Microsoft AI, collaboration, low-code, security and SaaS applications in a composable platform.
The company also announced the preview of Microsoft Supply Chain Center, a ready-made command center for supply chain visibility and transformation and part of the Microsoft Supply Chain Platform. Supply Chain Center is designed to work natively with an organization’s supply chain data and applications, with built-in collaboration, supply and demand insights, and order management.
“Businesses are dealing with petabytes of data spread across legacy systems, ERP, supply chain management and point solutions, resulting in a fragmented view of the supply chain,” said Charles Lamanna, corporate vice president, Microsoft Business Applications and Platform. “Supply chain agility and resilience are directly tied to how well organizations connect and orchestrate their data across all relevant systems. The Microsoft Supply Chain Platform and Supply Chain Center enable organizations to make the most of their existing investments to gain insights and act quickly.”
“Supply chain solutions are more critical than ever. Our early assessment of the Microsoft Supply Chain Platform and Supply Chain Center is that the company has put its technology, applications and resources together in a way that will serve its customer base well in a wide swath of IT and operations environments, offering flexibility for diverse IT environments and continuous agility for transformation into the future,” said Daniel Newman, founding partner and principal analyst of Futurum Research.
The Microsoft Supply Chain Platform: An open, collaborative and composable foundation for data and supply chain orchestration
With today’s announcement, we are making it easier for customers to realize the value of the Microsoft Cloud for their supply chain. The Microsoft Supply Chain Platform provides the building blocks across Azure, Dynamics 365, Microsoft Teams and Power Platform for customers to develop or independently adopt capabilities for their supply chain needs. With Dataverse, customers can create thousands of connectors to gain visibility across supply chain, develop custom workflows with low-code solutions in Power Platform, and securely collaborate internally and externally through the power of Teams. With tools and processes that drive positive impact, the platform can enable organizations to gain deeper insights and minimize the carbon impact of their organization and supply chain.
Subscribe to us to get updates and leave your comments below.
Photo by Turag Photography on Unsplash