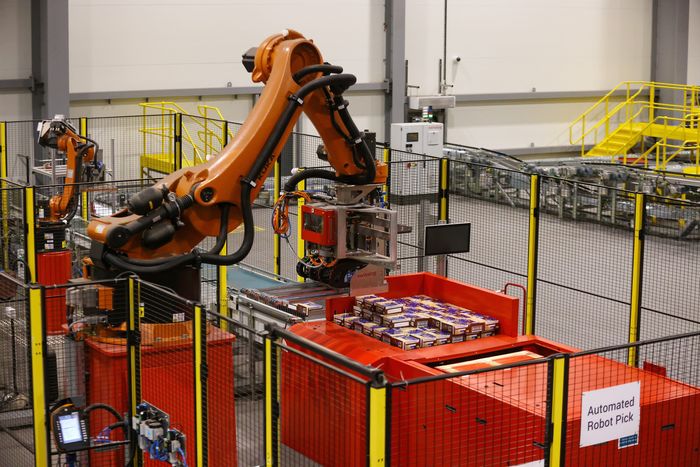
Nearshoring. Automation. Supplier diversification. Sustainability. Companies are adapting their operations to changing market pressures and geopolitics.
When a measure of strains on global supply chains fell earlier this year to levels last seen before the Covid-19 pandemic, it signaled to some that the product shortages, port bottlenecks and shipping disruptions of the past three years were over and that a new era of stability was on the horizon.
But industry experts say a “return to normal,” as the Federal Reserve Bank of New York described its Global Supply Chain Pressure Index in February, hardly means that companies are going back to conventional, some would say complacent, supply chains.
Instead, say academics and consultants, the experiences during the pandemic, along with changes in geopolitics, are leading to broader, potentially long-lasting changes in how companies manage the flow of goods, from the sourcing of raw materials to manufacturing and distribution.
The changes are playing out at factories in India, auto-assembly plants in northern Mexico, ports from the U.S. Southeast to East Africa and mineral mines in Canada and Sweden. The sites are where companies are implementing disciplines such as resilience, regionalization and supplier diversification that came to the forefront as they coped with the severe disruptions that began in early 2020.
The turmoil that began with the declaration of the Covid-19 pandemic first hit companies with sudden shortages of consumer staples as households locked down, was followed by factory shutdowns that interrupted the flow of goods and then hit transportation networks as an abrupt snapback in demand led to overstuffed ships and enormous backups at ports.
By April 2020, the New York Fed’s supply-chain stress index had shot up to double the level it reached during the recovery from the 2009 financial crisis. It finally fell back early this year to levels more typical of a measure going back 25 years.
“Some stresses have been taken off, there are fewer supply shortages, and things are a lot less hectic, but we certainly are not back to normal,” said Patrick Van den Bossche, a partner and global analytics practice leader at consulting firm Kearney. “There is a subdued level of urgency but a lot of things have changed.”
Read more at Here’s How Supply Chains Are Being Reshaped for a New Era of Global Trade
Leave your comments below and subscribe to us for a discussion.