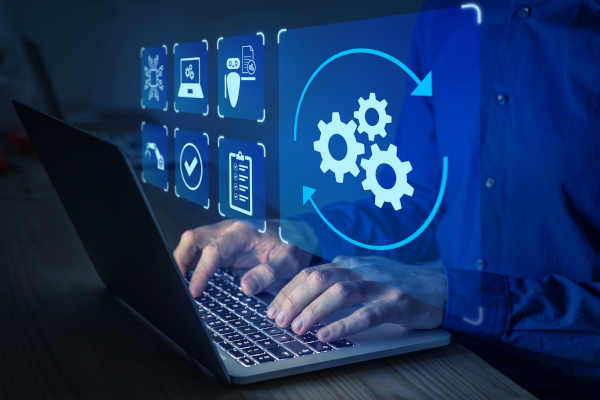
Robotic Process Automation (RPA) technology to automate business tasks with AI. Concept with expert setting up automated software on laptop computer. Digital transformation and change management.
Supply chain project management has evolved, shifting from a focus on efficiency to navigating a complex landscape influenced by globalization, technology, and changing consumer preferences. The vulnerabilities exposed during events like the COVID-19 pandemic underscore the need for adaptability. The pandemic posed challenges, disrupting production, leading to closures, and causing delays and increased costs in global transportation.
Additionally, unpredictable shifts in consumer behavior created demand fluctuations, impacting industries differently. Inventory management became more challenging, resulting in shortages or excess inventory. Supplier reliability and labor shortages further strained production capacity.
The crisis highlighted the necessity for digital transformation, remote work, and technology adoption in supply chain management. Regulatory changes and economic downturns added complexity to cross-border supply chains. Financial strain emphasized the importance of robust risk management, leading to a renewed focus on building resilient and agile supply chains. Businesses now invest in technology, diversify suppliers, and reassess inventory strategies.
Intelligent software enhances decision-making and risk management, facilitating collaboration throughout the supply chain. For instance, during sudden demand changes due to lockdowns, the software swiftly analyzes data, enabling real-time adjustments to inventory, production, and distribution. This adaptability ensures a responsive and agile supply chain, surpassing traditional approaches for efficiency and customer satisfaction.
The promise of intelligent software
In the current technological realm, intelligent software signifies more than just automation; it melds advanced algorithms, artificial intelligence, and machine learning to emulate human cognitive abilities. Unlike its conventional counterparts, this software learns, adapts, and autonomously recommends actions, excelling in data analysis and trend prediction. Its continuous adaptation based on feedback refines its performance over time.
How intelligent software could make a difference in specific situations
1. Demand volatility amidst global events.
The COVID-19 pandemic triggered significant demand shifts, straining supply chains. Intelligent software, with real-time analytics, could have monitored consumer behaviors, identified disruptions, and gauged inventory levels. Such insights would have refined demand forecasts, allowing organizations to adjust production and prioritize shipments, mitigating stockout risks and excess inventory costs.
2. Supply chain disruptions due to geopolitical tensions.
Geopolitical uncertainties can disrupt supply chains. Intelligent software could pre-emptively identify vulnerabilities, highlighting dependencies on specific regions or suppliers. Through simulations and alternative sourcing evaluations, it would have enabled organizations to devise resilient strategies, ensuring uninterrupted operations amid external disruptions.
3. Quality control and recall management.
Product recalls pose financial and reputational risks. Intelligent software, with advanced analytics, monitors production for deviations from quality standards. Using predictive analytics, it could anticipate issues, facilitating timely interventions, minimizing recall extents, and preserving brand reputation.
4. Transportation and logistics optimization.
Efficient transportation is crucial for supply chain success. Intelligent software, leveraging predictive analytics, would analyze factors like traffic and weather to optimize transportation strategies. This would reduce delays, enhance resource use, and boost supply chain effectiveness.
5. Inventory management in seasonal industries.
Seasonal industries face inventory challenges due to fluctuating demand and product perishability. Intelligent software, utilizing machine learning, analyzes sales trends and market dynamics to offer precise demand forecasts and inventory recommendations. This ensures optimal inventory levels, reduces holding costs, and capitalizes on market opportunities.
Leave your comments below for a discussion or subscribe to us to get updates.
Read more Transforming Supply Chain Management with Intelligent Software