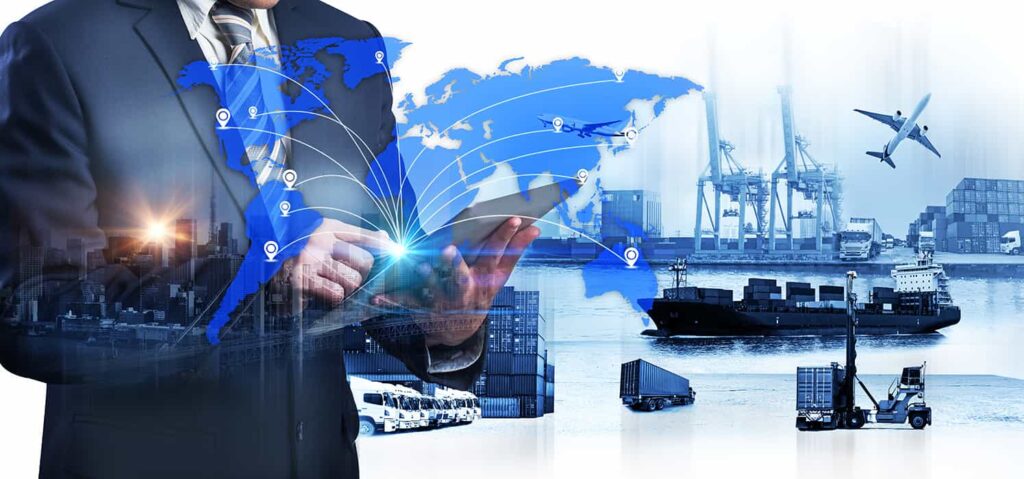
Technology investment fuels growth in supply chain finance.
According to a September report from Allied Market Research, “The global supply chain finance market was valued at $6 billion in 2021 and is projected to reach $13.4 billion by 2031, growing at a [compound annual growth rate] of 8.8% from 2022 to 2031.”
Technological advancements in digitalization and automation have made supply chain finance (SCF) more accessible and efficient, which has led to a proliferation of platforms and solutions that streamline the processing of invoices and payments, making it easier for companies of all sizes to implement SCF programs.
The increased complexity of supply chains makes managing working capital efficiently much more challenging. SCF can bridge the gap between payment terms and the actual flow of goods—helping buyers and suppliers improve their cash flow by accelerating receivables for suppliers and extending payables for buyers.
It is also a relatively safe investment in uncertain times. And it’s not just banks that are getting in on the act. Institutional investors view it as an attractive asset class; while fintech SCF platforms, often in collaboration with banks and other alternative investors, are increasingly helping to close the trade finance gap.
Regulatory changes, including changes in trade finance regulations such as the introduction of the UK’s Electronic Trade Documents Act of 2023, can encourage the adoption of SCF by reducing legal and operational barriers. It’s worth noting that there has also been a global trend toward SCF scrutiny. In the US, the Financial Accounting Standards Board issued an Accounting Standards Update in September 2022, which came into effect in 2023, requiring disclosure of key SCF program terms and obligations on the balance sheet in quarterly and annual reports.
There is also growing demand for businesses to identify and address human rights and environmental risks along their supply chains. For example, the EU’s 2019 Green Deal requires commodities traded through the EU and products placed on the EU market to be sourced and manufactured responsibly. Meanwhile, the EU’s Corporate Sustainability Reporting Directive came into effect in January 2023.
While consumers’ attitudes have significantly influenced environmental, social and governance (ESG) goals, vulnerabilities across global supply chains are forcing businesses to rethink SCF. Increasingly, SCF is being used as both an incentive and an enabler to encourage sustainability across supply chains, and both banks and nonbanks are increasing their sustainability-linked SCF offerings.
Sustainability is an integral part of MUFG’s mission as a company and a vital part of the bank’s identity. In addition to net-zero plans for its operations, MUFG has committed to investing more than $330 billion directly into sustainable finance by 2030. It also boasts of being the largest renewable energy project finance bank in the US, and it is the leading arranger of renewable energy globally.
“Within supply chain financing, we see companies at different stages of their ESG journeys depending on alignment between their procurement and sustainability teams, often with competing priorities and separate reporting lines. So, we meet our clients at their point of need no matter where they are in that journey,” explains Maureen Sullivan, managing director and global head of SCF at MUFG.
“Some clients face financial stress in their efforts toward net-zero emissions and need financing structures that enable their transition sustainably,” Sullivan adds. “For those clients, we offer transition SCF financing, where we ring-fence select suppliers that can provide sustainable improvements as the client transitions to a greener business model.”
“For clients further down the path,” she continues, “we provide financing incentives to drive positive supplier behavior. Based on their chosen KPIs, many companies want to use SCF to encourage and promote a sustainable and socially responsible supply chain. We offer an independent third party to evaluate a supplier with an ESG score and, based on demonstrated improvements over time, offer that qualified supplier a tangible incentive such as a more attractive financing rate. ESG scoring is tiered for small to midsize suppliers, while we create bespoke KPIs for large suppliers based on publicly stated long-term measures to access preferred rates.”
Recent global events, such as the Covid-19 pandemic and other ongoing supply chain disruptions, have highlighted the importance of building resilient supply chains. SCF can build this resilience by providing access to financial resources and improving cash flow management.
Overall, the growth of SCF is driven by a confluence of factors that make it an attractive solution for businesses of all sizes. Its ability to improve working capital management, build stronger supplier relationships, and mitigate risks in complex supply chains will likely continue driving its adoption.
Read more at World’s Best Supply Chain Finance Providers 2024
Subscribe to us to get updates or share your opinions below for a discussion.